国内首套全电机伺服驱动精密模压成形机研制成功
关键词:高精度玻璃模压成型机,全自动玻璃模压机,玻璃模压成型机,低熔点玻璃精密模压,全电机驱动精密模压成形机,玻璃模压非球面透镜,高精度数控玻璃模压成形机
我国科学家历经6年,研制出具完全自主知识产权的“全电机伺服驱动精密模压成形机”。相关研究成果的落地,有望突破玻璃光学制造技术、装备和工艺上的国外封锁。
近年来,随着光电行业的迅猛发展,玻璃光学器件的应用和需求越来越广泛。但目前国内的光学器件制造仍受制于日本、德国等发达国家。国内玻璃光学器件制造企业几乎依赖国外进口加工设备,并采用国外加工工艺。这成为长期以来,我国玻璃光学器件制造的最大“痛点”。
北京理工大学教授、国家重点基础研究发展计划“玻璃微纳阵列高效超精密模压制造基础研究”项目首席科学家周天丰率领团队,经长达6年的攻关,提出了全电机伺服驱动精密模压成形机的设计思想,并以此为基础研制开发了样机,通过技术攻关,形成了具有完全自主知识产权的玻璃模压加工工艺,可实现在可见光玻璃材料和红外玻璃材料上加工各种类型、各种尺度微结构阵列与自由曲面玻璃器件。
周天丰介绍,设备使用的工业控制系统,相比国外同类型设备所使用的可编程逻辑控制器,更利于对控制系统进行改写和调试以及对工艺数据的保存和导出。同时,使用电缸作为模压机的驱动元件,相比国外同类型设备较多使用的气缸,更有利于对模压速度和模压位置的精密控制。此外,设备还对加热模块进行了进一步优化,相比国外同类型设备,有更高的加热温度范围。
目前,课题组已完成国内首套产品的开发,成果已具备产业化条件,并已在航空航天、兵器、船舶及激光器制造有关单位投入使用。
光学微纳阵列是指一定数量微纳尺度的透镜或棱镜的排列组合,因其特殊的几何特征,而具有多种光学功能,在红外、可见光、紫外(UV)/极紫外(EUV)乃至X射线波段对光波的物理特性进行调控和利用,实现传统光学元器件难以完成的任意波面变换的光学功能,是在现代光学工程中重要的光学元器件。光学微纳阵列制造是利用一定工艺方法在光学材料表面上加工出特征尺寸在纳米/微米级的形状单元,并按照一定规律排列分布,具有形状可控、表面质量高和一致性好等特点。玻璃微纳阵列模压制造是指在高温下施加一定的压力将模具表面的微纳阵列形状复制到受热软化的玻璃表面上,经退火冷却固化,在光学玻璃材料表面结构出微纳阵列。该方法具有成形精度高、效率高、一致性好和加工成本低等特点,适合大批量生产制造,被认为是光学微纳阵列制造最有效的方法之一,具有极高的研究与应用价值。
不同材料,单元形态和周期尺寸的光学微纳阵列具有各种不同的光学特性,既可利用其成像特性,又可利用其衍射特性,实现光学成形、光传输和光传感等多种功能,使光学微纳阵列在诸多领域具有广泛而重要的用途,如近年来蓬勃发展的立体成像技术、通信互联技术以及超精密数控制造中至关重要的位置检测技术等。光学微纳阵列受应用需求的驱动,近十几年来,对微纳结构光学功能元件的高精度、大批量、低成本的加工技术需求越来越大。
玻璃精密模压成形技术(GMP-Glass molding press)最初由美国柯达公司于1982年提出,并用于非球面透镜生产。2000年,美国俄亥俄州立大学Yi和德国生产技术研究会(IPT)Klocke等通过计算机仿真计算技术和模具补偿技术提高了非球面透镜的成形精度。随后玻璃精密模压成形技术被日本东北大学和东芝机械公司推广应用于光学玻璃材料表面的微沟槽和微纳阵列成形制造,极大的提高了微小光学元件的加工精度、加工效率和微结构单元密度。
具体方法为:首先加工出微纳阵列模具,再将玻璃加热到玻璃转化温度以上使其软化,然后通过精确控制成形压力、成形温度和冷却速率等成形条件,将模具的形状完整而又精确地复制到玻璃表面上。每片玻璃微纳阵列光学元件从坯料加热、加压成形、慢冷退火到快速固化这四个成形阶段时间周期只需要1~3min,加工效率极高,一致性好。玻璃超精密模压成形技术是光学微纳阵列低成本批量制造的理想方法。
本项目通过前期新型模具材料的超精密微切削技术和光学玻璃材料的热模压成形技术的基础理论研究,实现大面积高密度玻璃光学微纳阵列的高效超精密跨尺度制造,建立光学微纳阵列这一特殊物理性能器件的创成新原理和制造新原理,并研制了全电机驱动高温精密模压机,相对于传统气缸驱动高温模压机,加工精度等各项指标取得了压倒性优势。该装置目前可用于玻璃曲面屏、非球面透镜、自由曲面透镜、微透镜阵列、微结构阵列等光学镜片加工,极大的减小了光学镜片、尤其是复杂微纳阵列结构光学器件的制造成本,并提升3D玻璃曲面屏、微光成像、微纳相机、高功率激光器等光学系统性能。
一、整体介绍
本设备由北京理工大学开发,由一部机床主体及一个控制台、一台水冷机和一个氮气罐组成,具体如下图所示。
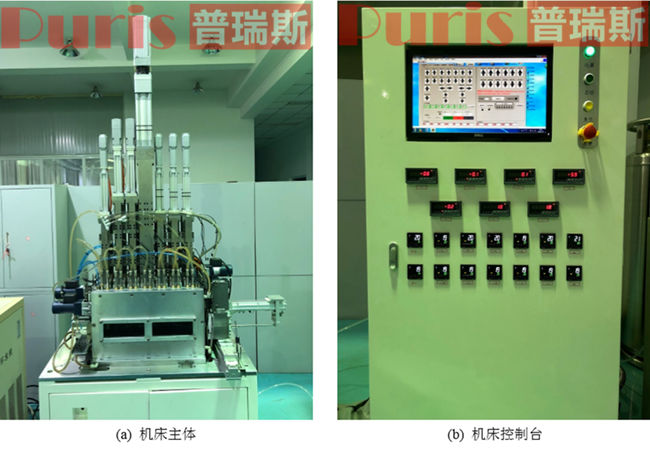
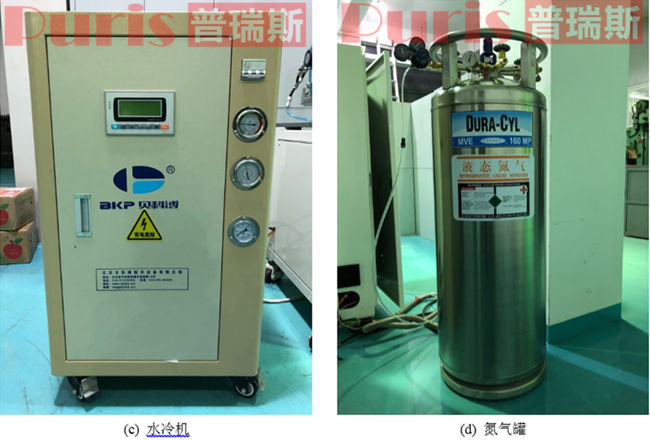
图1 全电机驱动精密模压机各部分示意图
本设备主要用于对光学玻璃、光学树脂以及其他可在较高温度下进行热压处理的材料进行高温模压加工,能够同时满足高校的研究需要以及企业内的批量生产需求。
二、机床详细介绍
本机的所有驱动元件(包括模压元件和进料出料元件)均为电缸驱动,因此不需要用于提供压缩空气的空压机或气泵等设备。但需要注意的是,电缸本身不能对输出力进行直接控制,因此模压工位上的电缸是通过与力传感器形成反馈关系来对输出力进行控制,因此本机实际能够达到的模压力的极限值和分辨率也以传感器的数值为准。
本机的控制台的核心为一部工业级PC,通过Windows系统运行以LabView环境下编写的控制系统来对机床的各部件实现控制。同时电缸的驱动器、各个继电器以及总电闸和各个子系统的电闸也被集成在了控制台内部。
本机通过在工位的上模压块和下模压块内插入加热棒和温度传感器实现加热及对温度的控制功能;同时本机通过水冷机将冷却水注入分布于机床主体内部的管道之中实现对机床主体的冷却,防止机床主体被加热过程中产生的高温损坏;同时本机通过氮气罐将氮气注入成形舱室内部实现一个氮气保护氛围,防止模具和预形体在高温下被氧化。
需要注意的是目前本机的温度控制系统独立于机床的整体控制系统之外,通过实体的温度控制/传感器来实现对六个工位的温度的控制与检测;冷却水通过水冷机的操作界面进行控制,并通过液体流量计实现对冷却水流量的检测;氮气可通过调整节流阀实现流量控制,并通过气体流量计实现对氮气流量的检测。
本机的加工舱室内总计有七个工位,自右向左依次为第1至第7工位。其中的第1、2、3工位为加热工位、第4工位为模压工位、第5、6工位为退火工位、第7工位为冷却工位。在一个完整的加工流程中,模具与预形体首先从机床右侧的进料机构送进加工舱室;然后首先在第1至第3工位上分步加热至模压指定温度,然后在第4工位上对模具施加压力从而完成对预形体的模压,进而在第5和第6工位上在保持一定压力的基础上慢慢降低温度,最后在第7工位上对模具和预形体进行快速冷却;完成加工后,模具和预形体从机床左侧的出料机构送出并由操作人员进行后续处理。需要注意的是,由于上述的功能需要,因此仅第1至第6工位具备加热及温度控制能力。
三、机床性能参数
- 模压用电缸参数
第1、2、3级电缸:
电缸极限压力400N、传感器捕捉范围0-200N、传感器分辨率0.2N
重复定位精度±10μm、极gg限行程100mm
第4级电缸:
电缸极限压力8000N、传感器捕捉范围0-5000N、传感器分辨率5N
重复定位精度±10μm、极限行程100mm
第5、6级电缸:
电缸极限压力1000N、传感器捕捉范围0-1000N、传感器分辨率1N
重复定位精度±10μm、极限行程100mm
第7级电缸:
电缸极限压力400N、传感器捕捉范围0-300N、传感器分辨率0.3N
重复定位精度±10μm、极限行程100mm
- 温度参数
机床的最高温度为800摄氏度
- 适用模具参数
本机床使用的模具的长和宽应分别限制在60mm之内,高度应被限制在45mm之内。
四、典型加工案例
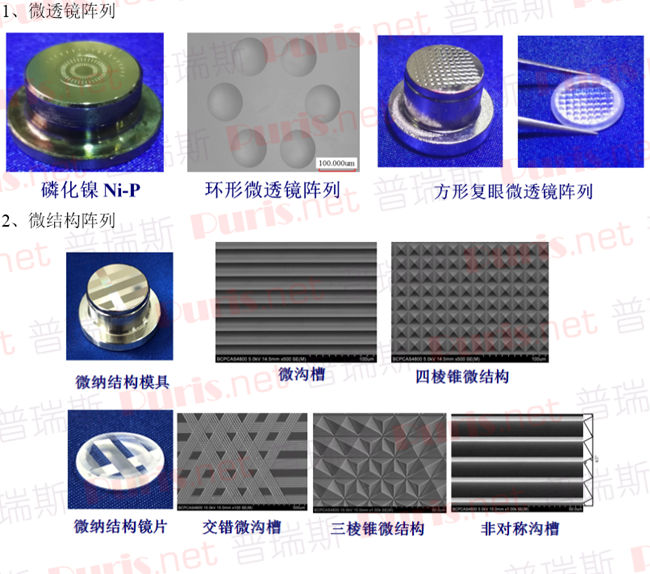
传统光学玻璃的加工,需要配合切割、抛光等多道复杂工艺,导致成品加工周期长,产能效率不高。以上技术可以通过模具压合光学玻璃,能加工各种复杂面型镜片,从而达到快速生产光学玻璃镜片的目的。
如果您对以上机床有兴趣,欢迎与我们取得联络~